3D CPS
The CPS range of 3D robot guidance systems was developed with the aim of offering the robot system integrator the tool best suited to his needs and capable of independently handling all the problems presented.
Observe
The 3D CPS systems make use of laser triangulation scanning technology (3D CPS 4.0) and coded structured light scanning technology (3D CPS FAST).
Both solutions are characterised by:
- sub-millimetre measurement accuracy
- minimal sensitivity to external light;
- high scanning speed
Find
3D CPS exploits sophisticated 3D pattern matching algorithms based on a ‘surface based’ approach.
The pattern of the set part is compared and ‘searched’ within the point cloud regardless of the colour of the object, ambient lighting conditions, and can even handle partially overlapping parts.
Choose
From all the parts found, the system chooses the one to be picked based on a series of parameters such as the regular emptying of the bin, the reliability of the gripper, and the possibility of reaching the part, grasping it and pulling it out along a collision-free trajectory. Once the part, the gripping point, and possibly the gripper to be used have been chosen, the 3D CPS sends the planned trajectory to the robot controller, which performs the picking without the need for the programmer to write any code.
Setting up a new Application
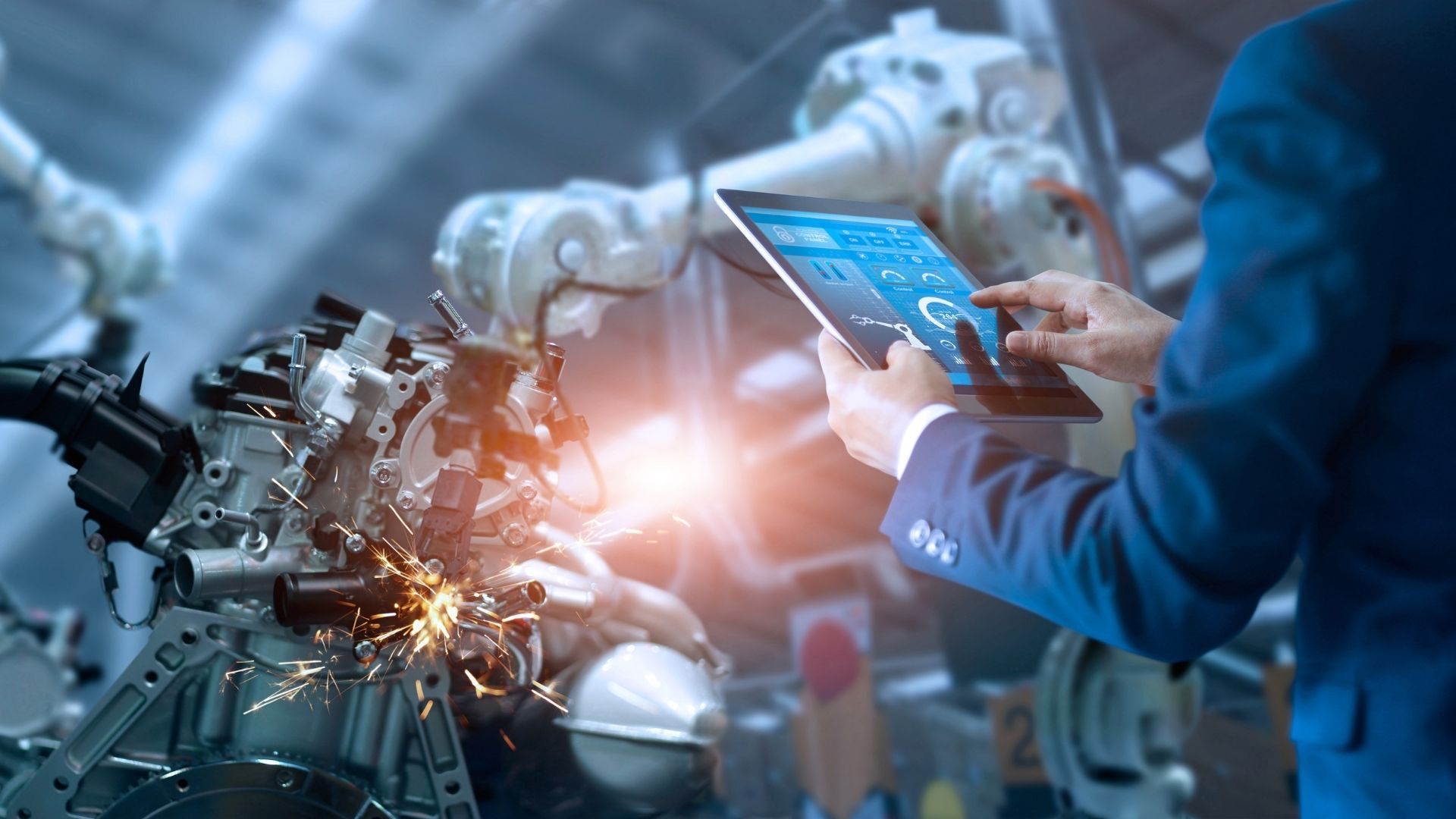
Configurator
The configurator is the tool with which, without writing any lines of code, the activity of picking up objects by robot is completely managed.
The operator must configure
- the three-dimensional environment in which the robot operates, meaning the model of the cell, the robot and the gripper complete with gripper fingers;
- the model of the part to be gripped, usually coinciding with a CAD view;
- the possible gripping points with their respective gripping modes.
Debugger
The debugger makes it possible to analyse the behaviour of the 3D CPS in order to identify any criticalities and eliminate them.
By importing a single file, the application makes it possible to visualise both the results of the process of recognising the parts randomly arranged inside the box, and those of the collision-free trajectory planning phase, which guarantees that the robot will pick up the parts correctly.
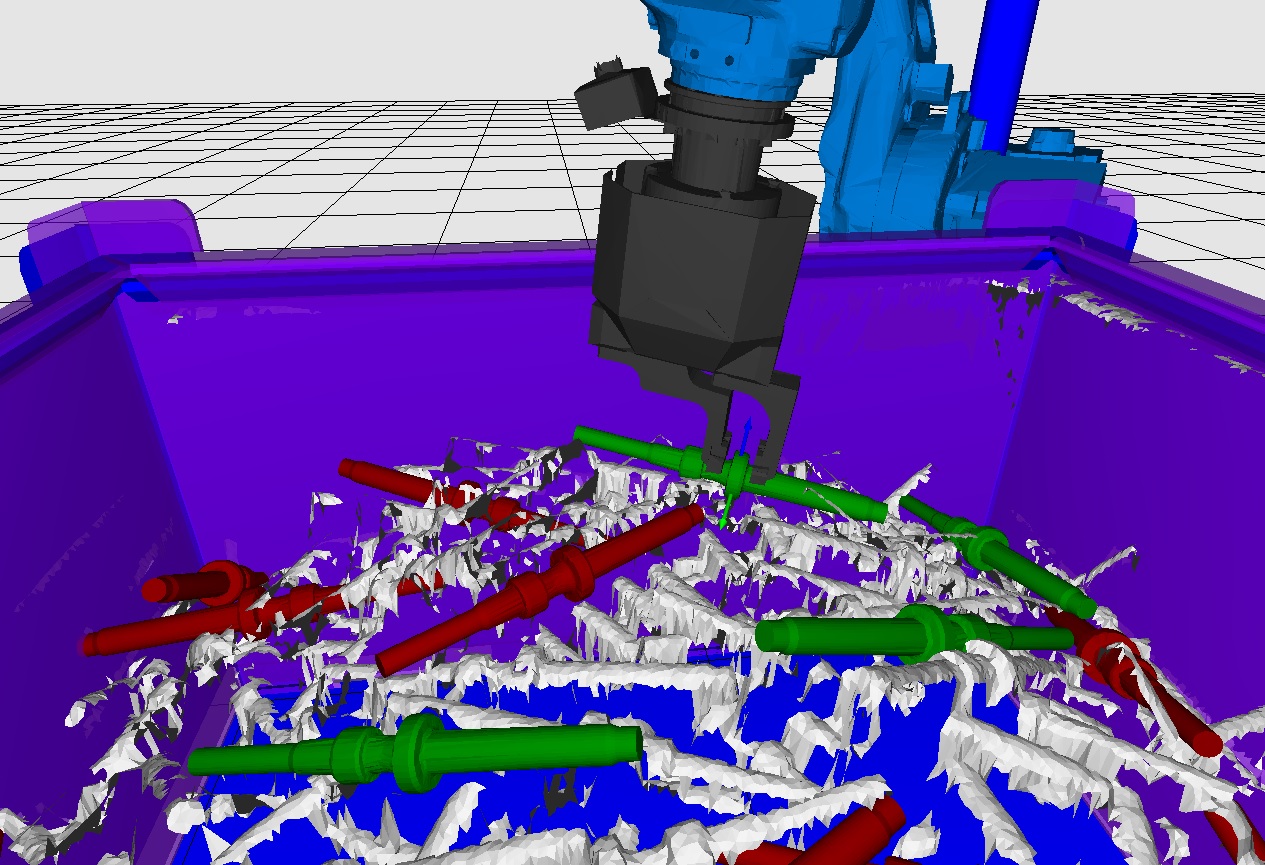